19/1 - Cut costs by choosing for synergy
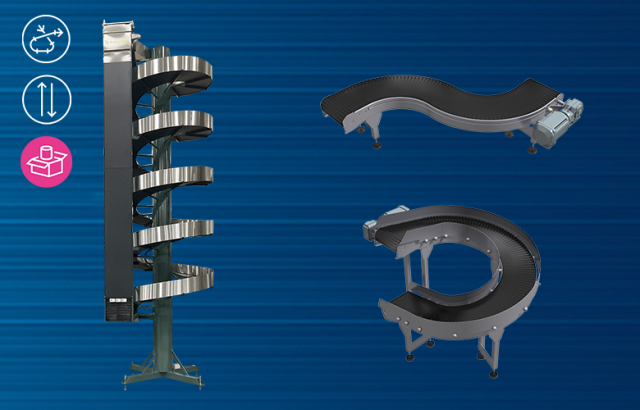
In any type of logistics or production layout, having the right synergy between the machines can improve efficiency while decreasing costs significantly. When machines work well together, everybody wins.
Details
- Same tech solutions with SpiralVeyor and Ambaveyor
- Simplify spare parts stock and maintenance training
- Lowers costs by cutting drives, transfers and controls
The end-user in this project is a pet food producer that wanted to open up floor space for additional inventory storage. The integrator responsible for the installation had already figured out that a spiral elevator combined with the smart use of regular conveyor parts should result in the most optimum solution. The only question that remained was deciding which technology to choose.
Many layouts are a collection of different brands and technology; all picked for their individual properties. But these lines can often benefit significantly from combining same-tech solutions. In general, it helps reduce the number of different spare parts and their prices while simplifying maintenance.
With the AmbaFlex family, the synergies are even better. SpiralVeyors can seamlessly extend and transfer to AmbaVeyor conveyors. As AmbaVeyor uses the same core technology as their Spiral counterparts, they can twist and turn effortlessly, offering unique shapes and curves. This resulted in more than 50% savings on the number of drives, transfers, and controls as it doesn't have to cut complex shapes into separate parts.
Looking for these types of synergy significantly increases efficiency. In addition, it reduces the costs of the line, both in the initial one-off investment and for the longer term, due to maintenance and parts.
AmbaFlex, elevating customers to greater heights!