14/8 - Replacing gravity chutes
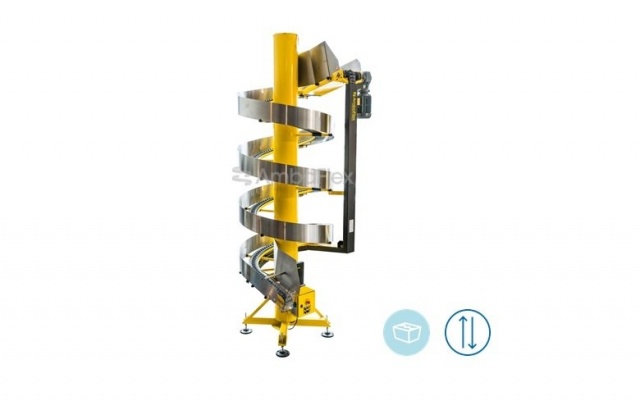
A leading internet retailer with distribution centers around the world recently installed a large number of AmbaFlex SpiralVeyor ToteLifts. Specifically designed to help achieve a flawless distribution process resulting in even shorter delivery times.
This particular retailer makes use of high mounted shoe-sorters throughout all of their centers. After the right products are picked and placed in totes, the sorters transport them to the next part of the process where they descend to a lower floor level. In the past, this retailer resorted to uncontrolled gravity chutes to transfer their products down. They quickly realized though, that this method did not meet their demanding quality standards.
The problem was not in the chutes themselves, but rather in the way they handled the totes descent. Heavy totes tend to speed up and hit the lighter totes resulting in damaged or lost goods. Which in turn leads to an increase in claims, costs, and delays.
This problem called for a “controlled”-chute, a spiral conveyor designed to handle totes with care when lowering them. One where a power driven belt makes sure all totes, regardless of their weight, will come down at the desired speed and avoid any of the collision issues in the downward transport of the totes.
The spiral conveyor specifically designed for jobs like these is the SpiralVeyor ToteLift. This spiral utilizes a unique belt type that provides a significant amount of added grip on the totes when compared to standard spiral conveyors. By doing so, the totes will not slip even when running at higher speeds, with a small radius, and at steep inclines. This solution will always deliver a controlled flow of items and recovers more than 50% of the space from the old sliding chutes.
One more proof of AmbaFlex’s leading position in Spiral Conveyor solutions!